Logistics blueprint supports strong growth at Active Ants
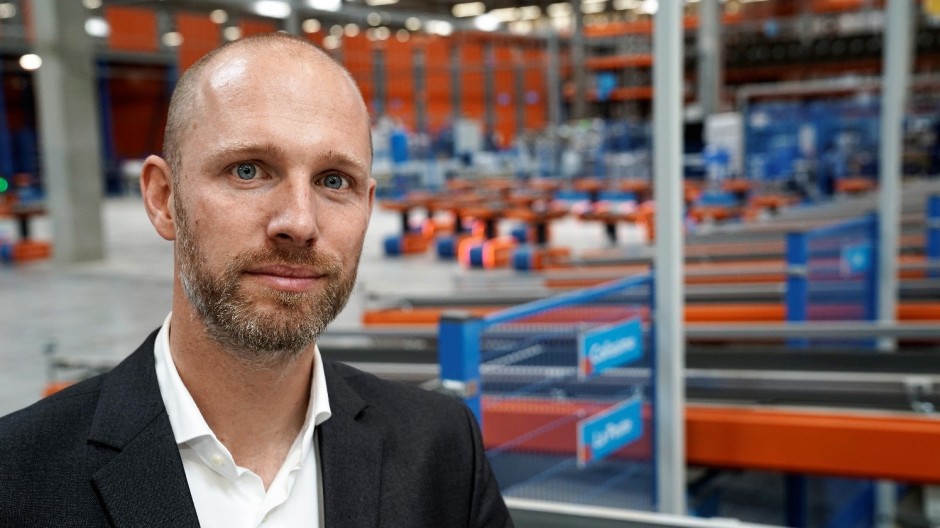
Interview with Wout Vuijk, international expansion manager at Active Ants
Active Ants has opened an ultramodern e-fulfillment center in Roosendaal, featuring a unique set-up where people and robots work efficiently alongside and with each other. The concept is serving as a blueprint for further expansion of the e-fulfillment activities in Europe and was developed in close collaboration with Groenewout.
Active Ants, a subsidiary of bpost group, provides e-fulfillment services for small and medium-sized online stores. “We operate from sites in the Netherlands (Nieuwegein and Roosendaal), Belgium (Willebroek), and Germany (Dorsten),” says Wout Vuijk, international expansion manager at Active Ants. In total, around 5 million orders are sent annually from the various sites to customers throughout Europe. And that number is still growing. To keep pace with this growth, Active Ants is set to open a new site in Great Britain (Northampton) in the autumn of 2022. A fulfillment center in France will follow in 2023. Together with Groenewout, the e-fulfillment company has developed a logistics blueprint that can be rolled out quickly and easily at the new locations.
Flexible and scalable
“The partnership with Groenewout actually started with one question,” says Vuijk. “We asked the logistics consulting firm what the most suitable packaging installation would be for our operation. That question then grew organically into a much wider study. Together we examined the entire process and arrived at the blueprint implemented here in Roosendaal.” At the heart of that blueprint is the AutoStore modular storage and order picking system.
In Roosendaal the system currently has 100,000 storage bins, which are continuously supplied to one of the picking stations by 100 robots. The transport to and from the AutoStore system is provided by flexible Autonomous Mobile Robots, or AMRs for short. “The AMRs work as a kind of flexible conveyor system. They handle the internal transport from the packaging installations to the picking stations and vice versa, but also from the box sealers to our shipping department,” Vuijk explains, adding that the concept offers several advantages: “Thanks to the AMRs we’re much more flexible. We can scale up quickly and easily when needed. Our employees also have less walking to do, so they’re more productive below the line. There’s a saving of valuable space too.”
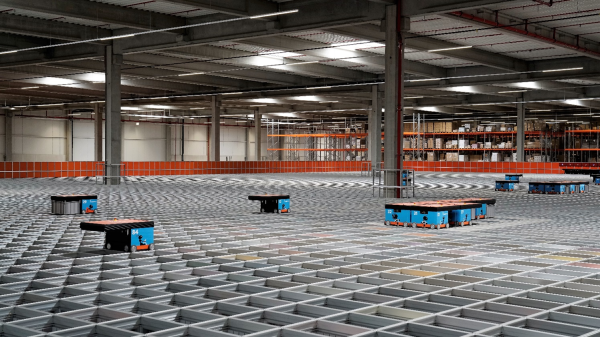
The goods-to-person AutoStore system is at the heart of the logistics operation and currently comprises 100,000 bins and 100 robots.
Impressive
The logistics handling looks as simple as it is impressive. As soon as an order from an online store enters the Active Ants system, a box is made to measure, taking into account the volume and weight of the order. That box is transported by one of the 65 AMRs to the correct picking station in the AutoStore system, where the ordered items are added to the box.
An AMR then takes the order box to the box sealing machine, where it is weighed and fitted with a unique printed lid. The shipping label is also printed on the box, so no adhesive is used. The completed order is then taken to the shipping department by an AMR and sorted for allocation to the correct shipper. “Because each box is tailor-made for the corresponding order, we do not need any filling material and an absolute minimum of air is transported in the chain,” adds Vuijk.
‘Perfect match’
“Without Groenewout's expertise things would have looked very different,” says the international expansion manager. “Their in-depth knowledge – in technology, IT, logistics trends, or other relevant areas – without doubt gives us added value. We also like their pragmatic and result-oriented approach. We can easily link up and communicate informally on the same level, so it’s a perfect match.”
Vuijk is already involved in a further expansion of the fulfillment activities. The blueprint certainly makes it easier for him: “The concept has proved its worth. But of course there are always details that require attention and adjustments. After all, every building is different in terms of architecture. In that respect, it’s never completely 'copy and paste' and it’s good to know that we can always rely on a partner like Groenewout to advise us on both logistics and architectural matters," he concludes